In practical applications, there exist a variety of welding methods for stainless steel, including manual welding, submerged arc welding, laser welding, and argon arc welding. Each welding method has its specific application scenarios and characteristics. To ensure optimal welding performance and quality, it is crucial to master the appropriate welding methods and techniques during the welding process. In this blog post, let’s take a closer look at the stainless steel welding methods and techniques.
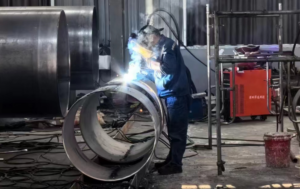
Stainless Steel Welding Methods and Techniques:
Firstly, regarding manual welding. Manual welding is one of the most commonly used welding methods, which involves the use of welding rods and arc welding machines. During the welding process, the welding rod generates an arc that heats and melts the stainless steel material, which then cools to form a weld seam. While this method is straightforward, the length of the arc needs to be manually adjusted by the welder. To achieve better welding results, it is necessary to select a filler material that is similar in composition to the stainless steel, ensuring better compatibility.
Secondly, there is argon arc welding. Argon arc welding employs argon as a shielding gas, surrounding the arc weld zone to isolate it from the atmosphere and prevent oxidation. Although argon arc welding offers high welding quality, it comes with higher labor and equipment costs, making it suitable for welding thin sheets or precision stainless steel parts. Compared to other welding methods, argon arc welding requires argon gas with a high purity level, preferably reaching 99.99%.
Thirdly, submerged arc welding is a technique that buries the arc beneath a layer of flux. This method offers fast welding speeds and high weld quality, but it can easily lead to segregation of alloy elements and impurities during the welding process. Submerged arc welding necessitates specialized equipment and flux, and it has strict requirements on the thickness of the stainless steel, making it suitable for welding stainless steel plates with medium thicknesses ranging from 6 to 50mm. During the welding process, it is essential to monitor the ammeter and voltmeter to ensure the normal burning of the arc and the quality of the weld.
Additionally, laser welding utilizes a laser beam as the heat source. Due to the optical properties of lasers, such as refraction and focusing, laser welding is particularly suitable for welding micro-parts and areas with limited accessibility. Furthermore, laser welding features low heat input, minimal welding deformation, and immunity to electromagnetic fields. However, laser welding equipment is costly, and the welding speed must be carefully matched with the laser power and the welding material. Excessive welding speed can lead to weak weld seams, while too slow a speed may cause burn-through or an excessively large heat-affected zone.
Summary
In summary, regardless of the welding method chosen, proper pre-welding preparations are essential. This includes surface cleaning to remove impurities like oil, rust, and dust from the stainless steel surface. Additionally, selecting suitable welding materials based on the type and thickness of the stainless steel is crucial. Pre-determining the welding sequence is also important to avoid issues like welding deformation and stress concentration.
Why Choose Sino Stainless Steel?
Thank you for reading our article and we hope it can help you to have a better understanding of the stainless steel welding methods and techniques. If you are looking for suppliers and manufacturers of stainless steel, we would advise you to visit Sino Stainless Steel.
As a leading supplier of stainless steel products from Shanghai China, Sino Stainless Steel offers customers high-quality stainless steel coils, stainless steel strips, stainless steel sheets, stainless steel plates, stainless steel bars, stainless steel wires and stainless steel tubes at a very competitive price.
b9tLCMhCcBI
STlxBYXfQCl
vPwENUmIDIm
x3PaF84RjR3
ZTDm7BGKeaB
k1Y6SKbqivs
pFJsyXfFAF2
4rLqOo21fVu
ZGJLBI4TWo1
MTrpd7Gtz8b
fL4yeWPDkXB
8HLx32w2JRX
FXS1PW3ymdM
T2y74JDd8wl
cc1tg1j8fG7
Rmom4zqQioa
rAadL5LXi11
7aI0acVN6e7
AoQEDAVHWFx
0PnyuBVHIqi
L2n8ADPNwTc
axm90yho6sq
NLTBpSZlqox
wq1LskVgyHo
vz4L1GzT3ro
vbYRyQNi5Xx
opuvR1xaiDZ
wUAcm1BjgNB
JZVyybWHhY8
5CWspnJPi7o
N5Ic8NAV75q
oGsQRXHo7CU
Mz4cML7oRT7
V7xXyqowKhK
3I9hM2H9J2d
TyiuAFb7MCS
iXs5tZGR9UH
ksmzMK2AjMv
irjIuvAEq9Z
jYpDw7TcWpi
Thank you for your sharing. I am worried that I lack creative ideas. It is your article that makes me full of hope. Thank you. But, I have a question, can you help me?
A Comprehensive Guide To Post Cycle Therapy
HSMD
### A Comprehensive Guide To Post Cycle Therapy
HSMD
**What Is Post Cycle Therapy?**
Post Cycle Therapy (PCT) is a period of time spent
after a course of hormone therapy, such as Testosterone Replacement Therapy (TRT), where individuals monitor their hormones to ensure they are within a healthy range.
This approach allows for adjustments in dosing and helps prevent long-term complications
associated with hormone imbalances.
**Is Post Cycle Therapy Necessary?**
Yes, PCT is crucial for anyone undergoing TRT or other forms of hormone
replacement. It ensures that the body doesn’t become dependent on external
hormones and helps maintain natural hormone production over time.
Without proper post-cycle monitoring, individuals may experience negative side effects or long-term health issues.
**The Importance of Sleep and Rest during PCT**
During PCT, adequate sleep and rest are essential for recovery and maintaining hormonal balance.
Sleep regulates hormones like cortisol and ghrelin, which play
vital roles in metabolism and recovery. Poor sleep can disrupt
these processes, leading to irregular hormone levels and potential health complications.
**When Should I Start Post Cycle Therapy?**
Post cycle therapy typically begins after a full course
of TRT or other hormone treatments. The duration varies depending on the individual’s needs and the
recommendations of their medical professional. It’s important to follow a structured plan to avoid missed windows for monitoring.
**How Long Does PCT Last For?**
The duration of PCT can vary from several weeks to months, depending on the hormone being used and the patient’s health history.
A personalized treatment plan is often recommended to ensure
safety and effectiveness.
**Why Should I Have Post Cycle Therapy at Harley Street MD?**
Harley Street MD specializes in personalized post cycle therapy
programs tailored to individual needs. Their expert
team of endocrinologists and healthcare professionals ensures
that each patient receives the highest standard of care, monitoring, and support throughout their recovery journey.
**Evidence-Based Research and Studies**
Research has shown that post cycle therapy significantly reduces
the risk of hormone-related side effects and restores natural
hormonal function. Studies have emphasized the importance of PCT in minimizing
long-term health complications associated with TRT.
**Book An Appointment**
At Harley Street MD, we understand the importance of personalized care.
To book an appointment or learn more about our post cycle therapy programs, visit
Your Website URL or contact us directly. Our team is here to help you
achieve optimal health and wellness.
**Recent Posts**
– Exploring the Benefits of Bioidentical Hormone Replacement
Therapy (BHRT)
– Understanding the Link Between Sleep and Hormone Balance
– The Role of Diet in Post Cycle Recovery
**Who We Are**
Harley Street MD is a leading medical clinic dedicated to
providing innovative solutions for hormone-related conditions.
Our team of experts combines cutting-edge knowledge with compassionate care to
help patients achieve their health goals.
**What We Do**
We specialize in post cycle therapy, TRT, and other hormone replacement treatments.
Our programs are designed to restore hormonal balance, enhance well-being, and promote long-term health.
**Opening Hours**
Monday: 8:00 AM – 6:00 PM
Tuesday: 8:00 AM – 6:00 PM
Wednesday: 8:00 AM – 6:00 PM
Thursday: 8:00 AM – 6:00 PM
Friday: 8:00 AM – 6:00 PM
Saturday: 9:00 AM – 5:00 PM
Sunday: Closed
For more information or to schedule an appointment,
visit Your Website URL or call us today.
You will likely preserve any energy, muscle, or athletic features achieved with
creatine supplementation. Nevertheless, you may not see any continued improvements
in athletic performance. The only time you would possibly wish to have a look at a different variation is when you have problems with bloating, which some folks claim
they get with creatine monohydrate.
It’ll be available as anhydrous creatine (100% creatine), traditional monohydrate
creatine (90% creatine and 10% water), and even micronized creatine (improved water solubility).
Leslie has been passionately involved within the health and
fitness industries for over a decade. She is consistently reviewing
the most recent scientific research and research to be able to take a research-backed method to lifestyle optimization. Leslie shares her findings on Fitness Clone to
help different well being enthusiasts select the products
and routines that can help them achieve their goals.
The cleanliness of this product is certain going to satisfy
demand from those wanting ahead to taking benefit with out having any issues about elements or purity.
Bottom line is if you are on the lookout for the top pre-workout with creatine, BlackWolf must be on the top of your list.
This complement incorporates all of your typical pre-workout components like L-Citrulline, Beta-Alanine, Betaine Anhydrous,
and Taurine. Every of the 5 types of creatine has its personal distinctive properties, so combining all of them collectively provides you a complement
with extra intensive benefits. In our opinon, if you want to build
strength and muscle, Creatine HMB is the finest choice. With 13+ years of expertise as a personal coach, 5 years as a
NCAA Power Coach at Ny University, and over 550+ printed fitness and diet articles, he knows a thing or two about fitness.
He also holds a masters in Exercise Physiology from Columbia College and a bachelors in Train Science from Bowling Green State University in Ohio.
Liquid creatine is simply that – creatine that was already dissolved in water.
If you wish to merely drink your complement, liquid creatine
might work better for you. Creatine monohydrate is the most generally used kind of creatine available in the market.
It can also be essentially the most researched type of creatine – and quite a few research agree that creatine is protected to make use
of.
When athletes bulk, they aren’t simply growing their muscles by consuming extra food.
If you wish to bulk up fast, micronized creatine is one of the simplest ways to do it naturally.
It’s an amino acid already in your physique, and multiple studies have proven that taking more creatine is totally safe.
At USD 0.33 for the massive pouch, it provides glorious worth for cash.
It’s a simple and clear creatine that is our best creatine for women. Nonetheless, bear in mind
that while Promix makes use of third-party testing,
the organization isn’t specified on the pouch.
Yet, our standout alternative for one of the best creatine complement is Onnit Creatine Monohydrate.
Onnit creatine holds the Informed Sport Certification, is uncomplicated, and free of sugar.
With Onnit Creatine, you get 5 grams of micronized creatine monohydrate per serving, with none additives.
This powder has been my creatine supplement of choice for almost two years,
and I’ve been impressed with how it performs. It mixes easily, is truly tasteless, and would not have any of that gritty texture creatine powders can sometimes have.
Are you on the lookout for maximum muscle progress on the health
club however having trouble bulking up?
Let’s break it down in a method that’s straightforward on the pockets and the mind.
Creatine is actually one of the extra budget-friendly supplements out there, but
the price can change based on what sort you’re after and what else
may be blended in. A Quantity Of types of creatine are out there, and one
would possibly suit you better.
Many folks take dietary supplements to increase their ranges of creatine as
a end result of it might be very tough — and
expensive — to get enough from food plan alone.
Nutrabay Pure Creatine Monohydrate is an reasonably priced and efficient possibility for these
trying to enhance their muscle gains without breaking
the bank. This unflavored, one hundred pc pure creatine mixes easily into water or your favorite protein shake.
Its simple formulation, free from synthetic components or fillers, makes it a
dependable alternative for athletes focused on quality
and affordability. It is scientifically confirmed to extend muscle mass, strength, and mind function. The excellent news is this has solely been shown short-term or within the first few days of a loading section of creatine at 20 grams per
day. Stangland stated that after those first days, the whole physique water returns to its regular state and
hasn’t proven any overall weight acquire because of creatine supplementation.
Whether Or Not you are a bodybuilder, athlete,
or fitness enthusiast trying to maximize your gains, MuscleTech Platinum Creatine Monohydrate is a stable
choice. Optimum Vitamin Micronized Creatine Powder is a highly trusted
and widely used complement among athletes and fitness lovers.
It accommodates pure creatine monohydrate, which is
understood for its effectiveness in enhancing muscle energy, energy,
and overall athletic efficiency. This micronized
kind ensures higher solubility and absorption, making it simpler to mix into drinks or
shakes. Whether Or Not you are a newbie or a seasoned athlete, this creatine powder can be a valuable
addition to your workout routine. Selecting the best creatine product can have a big impression in your efficiency and general health targets.
This is probably the most extensively studied out of all the kinds of creatine and it proves to be efficient
and protected time and time again. It’s composed of 1
compound which typically comes in a powder form.
In different words, there aren’t any proprietary blends or particular
ingredients that you need to concentrate to.
Their supplements bear thorough in-house testing for banned substances.
Nutrigo Lab Power is a dietary complement formulated that can help you change your physique earlier than getting right down to intensive exercises.
The supplement features strength and power-enhancing elements that will assist you prepare harder than earlier
than. Loopy Diet Final CRN-5 Creatine Formulation is a dietary complement designed that can assist you improve your hydration, energy, energy, and restoration.
The complement options 5 various kinds of creatine for
a 5x intensity workout without loading, cycling, or bloating.
In this review, we have mentioned in detail our greatest creatine
dietary supplements together with their advantages.
You’ll discover creatine monohydrate, both in powdered or capsule type, flavored or unflavored, at your vitamin retailer,
so you presumably can decide based mostly in your preference.
Although creatine can be found in smaller portions in foods like salmon, hen, beef and
pork, many individuals take supplements for fitness benefits.
Nevertheless, did you know that creatine also can produce other
results on each your mental and bodily health?
To learn more, we spoke with experts about creatine’s advantages, results on weight, outcomes and how to choose on the proper complement.
Creatine is secure to take every day as lengthy as you follow the
instructed daily dose of 3–5 grams.
On workout days, it is suggested to take creatine shortly earlier than or after exercise.
On rest days, it may be useful to take it with meals, but the timing just isn’t as crucial as on exercise days.
Creatine is of course produced by the physique, so there is not a recommended consumption from the
FDA. Nevertheless, consuming sufficient amounts of protein is essential
for creatine manufacturing. Analysis suggests that 10 to 30 percent of
your complete caloric intake ought to come from protein sources.
Creatine ethyl ester is another newer form of creatine that’s extra simply absorbed by the physique than monohydrate.
Some folks might notice a little bit of weight achieve caused by
water retention after they begin taking creatine.
It Is totally regular and really a half of how creatine powers
up your muscles. Don’t worry too much except there’s a big change in your body weight.
Some research even compared monohydrate to different types of creatine, and—you guessed it—creatine monohydrate got here out on prime.
One such study showed that efficiency in cyclists elevated by 10% when utilizing monohydrate,
and no increase in performance was shown in those who took fancy, spendy liquid creatine.
In this examine, even though an increase in DHT was shown, it nonetheless stayed nicely inside the regular vary.
So even if creatine did increase DHT in this case, it in all
probability wouldn’t have had rather more of an effect on hair loss than would have in any other case occurred.
Creatine monohydrate is usually well-tolerated, but some individuals could
expertise side effects like weight achieve as a result of water retention, digestive issues,
or muscle cramps. It’s necessary to comply with beneficial dosages and
seek the advice of with a healthcare provider when you have any concerns.
The runner-up, Bageto, however, sticks to a basic creatine
monohydrate kind. Whereas it lacks micronization, you’ll still
get the core advantages of creatine—just at a slower
absorption rate. Both manufacturers are high quality choices,
but EcoWise’s formulation may be higher if you’d like a quicker uptake.
Anticipate noticeably improved endurance and enhanced
muscle restoration with constant use. Many customers report feeling much less fatigued
mid-workout, making it simpler to push by way of additional reps.
And visually, you’ll likely discover a
fuller muscle look due to elevated hydration.
As a further bonus, Muscle Memory contains 150 mg of peat and apple extract,
labeled as EleATP, which is clinically proven to additional bolster ranges of
ATP in the body. Proponents of Ora’s muscle reminiscence claim its texture circumvents the stereotypical grittiness usually present in different creatine powders and it has a “pleasant”
Acai berry taste, which was developed by a chef.
Maybe the most important factor when deciding what creatine supplement to purchase is its purity; principally, how much filler are you getting?
The excellent news is that with so many products
in the marketplace today, it’s fairly protected to say that the vast
majority of creatine powders are going to have very high purity.
Crazy Nutrition’s Ultimate CRN-5 creatine formula stands out
as a dependable and effective alternative for athletes seeking to optimize their efficiency and improve their workout results.
It’s not cheap in comparison with the others, however it does
come with the potential for better absorption, as well as the added advantages from the electrolytes.
Plus, it uses pure elements and non-artificial sweeteners so it tastes
good.
“It felt like a pure efficiency enhancer,” mentioned one tester,
adding that they had more energy for their exercises, without experiencing any nasty unwanted effects like anxiety or overheating.
Other panel members agreed it made them really feel
more powerful throughout exercise, with many saying they might continue to make use of it following the trial
period. The taste was nice, and the feel was easy when stirred
into water. A few testers famous that the instructions on the again of the packet
had been too small, and some had issues with resealing the pouch, however these
are minor quibbles. Creatine is generally safe for healthy adults to make use of for weeks or months and doubtlessly for years.
Research constantly demonstrate the security
of creatine supplementation at frequent dosages, including excessive doses of 20 grams per day for as much as seven days and 3-5 grams per
day for a number of weeks to months. Creatine could cause weight gain because of water retention,
particularly within the early phases of supplementation and when taken at high doses.
Always choose a powder over a gummy (here’s why),
look for creatine monohydrate, and choose for one that provides 3 to 5 grams per serving.
And research shows that leaning on a day by day creatine complement is the greatest way for everyone
(vegetarian and omnivore alike) to fully maximize
their creatine stores. Research show that when your body’s creatine shops
are full (aka saturated) it actually does assist you to obtain that
goal.
Alongside this, it has a small quantity of energy, which principally comes from the added maltodextrin. This is a type of processed carbohydrate commonly used as a thickener and bulking
agent. Whereas it does are available in two tub sizes, the lack of flavor choices is something that future formulations may improve on. Nevertheless, this makes it appropriate to be combined with a wider range
of different dietary supplements. Each tub provides glorious transparency, clearly displaying
the components alongside the Informed Sport approval stamp.
The best general, EcoWise, gives you the selection of mango and strawberry,
good for anyone who likes a little bit of selection. The runner-up, Bageto, keeps it easy
with blended berries—a favourite among clients. And it’s made in a cGMP, FDA-registered
facility and third-party examined.
Most girls discover that after reaching desired outcomes, reduced frequency
of use (2-3 instances weekly) helps preserve improvements.
Targeted strength training routines designed to develop the pectoral muscles underlying breast tissue.
Creatine gummies supply a easy and practical answer for those in search of some great advantages of creatine
with out the trouble of powders or tablets. Infused with delectable pure fruit flavors, these gummies can be consumed at any time and place with ease.
Appropriate for those with dietary restrictions, Onnit
Creatine Monohydrate is free from dairy, soy, and
is vegan-friendly. It is an reasonably priced option for many
who need to try creatine for the primary time, particularly as it is out there
in a compact container.
And when combined with common pre-workout components,
it may lead to different workout efficiency advantages, such as extra energy and endurance.
When you perform high-intensity activities like weightlifting or sprinting your muscle demands quick bursts of energy.
Creatine powder helps in growing muscle mass, bettering strength
and energy, enhancing athletic efficiency and aiding in faster recovery between workouts.
In the quest for optimum athletic efficiency, selecting a creatine
complement that ensures purity and effectiveness is essential.
“Making positive you may be consuming water helps the intracellular means of how creatine is used to make power,” says
Stangland. How shortly you will see results is dependent upon a number
of elements, together with food regimen, lifestyle habits,
coaching regimen and frequency of creatine supplementation. That stated, you could
discover improved muscular endurance and power inside
every week of constant use. Extra appreciable adjustments, corresponding to increased muscle volume, sometimes
take 4–6 weeks of normal use. When used at the beneficial
every day dose of 3–5 grams, creatine dietary supplements are generally well-tolerated and unlikely to trigger unwanted effects.
Nonetheless, higher doses, corresponding to those used during a loading phase,
may lead to gastrointestinal discomfort. Frequent issues embody bloating, diarrhea or nausea, which typically subside once the
dosage is adjusted.
Besides taste, Recharge stands out as a great choice for post-workout restoration. In addition to creatine, the powder consists of L-carnitine L-tartrate, an amino acid type that is been proven to
help muscle recovery and soreness after train. The powder
also contains corosolic acid, a natural plant
compound that will help enhance insulin resistance and support nutrient uptake for
mobile energy. The greatest creatine supplement for muscle development contains the most effective type
of creatine and comes from manufacturers that guarantee the
greatest purity of their manufacturing and testing practices.
In addition to owning and working UPCF, Jon applications and trains athletic groups
and is the non-public trainer for several professional athletes.
Jon honed his management and coaching abilities over the previous 14 years progressively gaining
larger roles with a major company. Throughout his career he always made time to volunteer
coach sports activities teams whereas sustaining an active recreational life-style together with his household.
Jon is the head coach of the UP Viks 5th grade soccer and president of the UP Vikings Lacrosse Club.
The state-of-the-art facility presents cutting-edge amenities, ample parking,
and accessibility for attendees, making it a perfect location for large-scale gatherings.
Positioned in the heart of Big Apple, Albany presents a
super setting for the CrossFit Games, combining accessibility,
world-class services, and a vibrant, welcoming atmosphere.
While this will sound like a recipe for turning into muscularly imbalanced, the other seems to be true.
This is probably going as a result of power features come from
larger muscles (hypertrophy) and our nervous system’s capacity to coordinate muscular tissues to work collectively (neural adaptations).
A measured strategy can pay dividends because the exercise progresses.
Remember, this primary round is when all of that adrenaline and anxiousness will kick in—stay
in control. This final fitness check is a combination of grip, tempo, and method.
As fatigue sets in, movement breakdowns turn out to be more frequent,
resulting in no-reps and wasted energy.
While many grips are manufactured from leather, these are made of Kevlar.
It’s abrasion-resistant, so the grips won’t deteriorate shortly.
They’re not machine-washable, but you can hand-wash them with
gentle soap and heat water and lay them out to air dry.
For some, the Open is an opportunity to test their fitness and see how much fitter they’ve turn into over the
past yr. For others, the Open is about placing themselves out there, exhibiting up, and
celebrating fitness and connecting with others of their affiliate and around
the globe. For a choose few, the Open is the first step in qualifying for
the CrossFit Games. Sure, Karen, when you go to the Open web
site there are scaled variations for Masters.
The weights drop to seventy five,55,& 35 respectively & the wall walks usually are not flush to wall.
Might you please e mail with the steps you adopted when making an attempt
to submit your score? We recently carried out a repair on Android (v 3.sixty five.1)
that addressed related issues skilled by different users, so we recommend updating
to the newest version of the applying and trying
once more.
For instance, slight adjustments in squat variations,
as proven beneath, can considerably change physique positioning.
Attain out to your nearest CrossFit gym to ask about their
schedule, prices and how to get started–some may
even supply a free trial. Not everybody can deal with the Rx version of 25.three, and that’s okay.
The Open is about participation, pushing yourself,
and bettering over time. The preliminary spherical could really feel
manageable, but resisting the temptation to go all out is
crucial.
Christy has lived in College Place for the past 18
years and is worked up to be working for a gym that is serving to to convey the
community together to enhance their well being. Growing up Christy was a competitive gymnast and has continued to take pleasure in difficult herself physically into maturity.
Prior to beginning CrossFit she was an avid long distance runner, practiced
yoga often and loved boot-camp fitness classes. Her want to push herself is
what introduced her to the game of CrossFit.
Just click on the beneath button and select the most suitable session for
you. A coach shall be there to welcome you and reply any questions you may have.
If you’ve any questions earlier than you book then contact us right here.
You start with good intentions, stick with a program for a few weeks
after which find yourself getting bored, losing motivation or not seeing the outcomes you’d
hoped. Stay up to date with the most recent insights,
specialists suggestions, and confirmed strategies
to enhance your powerlifting efficiency and elevate your
strength coaching journey. If you’re in search of much more hand protection when doing pull-ups outside of a CrossFit
WOD, try our favorite pull-up gloves.
On this blog we share all of the issues we wish we knew when getting began.
On a personal stage, I’ve been dedicating myself to the world
of powerlifting for the past 15 years, having each competed and coached on the highest degree.
The best CrossFit grips are the Bear KompleX 2 and three Hole
Carbon Hand Grips as a end result of they’re durable, have a cushty wrist strap, and
supply a wonderful grip on the bar. If you already have an open tear
in your palm, CrossFit grips can add a protective layer to stop
it from worsening.
Additionally, comply with the manufacturer’s directions
for the way to retailer and wash them to spice up their longevity.
With their help and expertise I was able to rank ninth in the Usa in my age group on the CrossFit open games.
The community connections you make will help keep you
accountable and inspired. Tickets for the 2025 CrossFit
Video Games will go on sale in early spring.
CrossFit has teamed up with JPG Travel/Event Pipe to supply discounted resort lodging for the 2025 CrossFit Video Games.
The 2025 CrossFit Video Games will happen at the MVP Enviornment in Albany, Ny, from Friday,
Aug. 1 to Sunday, Aug. 3.
For those with sensitive skin or those who are
just in search of a comfortable pair of grips, the PICSIL Azor grips match the bill.
They function a delicate, breathable micro-perforated
materials and an anti-allergy Velcro strap to help reduce irritation on the arms
and wrists. We help people attain their private and bodily goals via brief, significant exercises tailored to you.
This ultimate technique applies when a muscle or joint can’t be used at all.
The adhesive is sticky and will stay on your hand even if your palms get
sweaty, and the fabric absorbs chalk nicely when you need it for a fair better grip on the bar.
For scaled athletes, wall walks are modified with
a 55-inch goal quite than the RX distance. The barbell weights lower, however the construction remains the
same. The combination of barbell movements and wall walks can tax your grip.
With years of success and expertise, we are capable of
analyzing your body and making a fitness plan that may allow you to reach your targets.
Most plans include wholesome consuming and exercise, to ensure one of the
best outcomes for our patients. We will work
with you to keep you on monitor and motivated to achieve your objectives.
They’re less expensive than different choices but still plenty sturdy.
The cheap price additionally makes these the most effective
CrossFit grips for newbies who don’t want to spend a lot
of money on extra premium grips just yet. Nonetheless, you will get at least a year’s
value of use out of the Bear KompleX Carbon 2 and 3 Hole Carbon Hand Grips, depending on how usually you
employ them. Different grips only last a couple of months earlier than you want to exchange them.
I even have done things physically I never thought was possible however more importantly it’s the people and
the mental piece. It affects your training
contained in the fitness center and your life outside
the fitness center.
We provide coaching that has offered real outcomes
to hundreds of individuals. WodPrep simply
dropped their latest Instagram publish, breaking down what we would see in CrossFit
Open 25.3—and their evaluation makes a lot of sense.
By looking at past exercises, movement tendencies, and gaps in what’s been tested thus far, they’ve made an informed guess about what’s coming next.
Another effective strategy is limiting your vary of motion to avoid painful positions.
Whereas training by way of a full range of movement is right when healthy, partial-range coaching remains useful when essential.
A easy way to train round an damage is to use a variation of the affected motion sample.
You shouldn’t necessarily go for the most affordable possibility you’ll find.
They could also be made of lower-quality materials and wear
down sooner than grips that value more. However as soon as you find grips you take pleasure
in, be positive to can afford to switch them each 4 to six
months. They require extra chalk as a end result of they’re not as grippy, especially in the event that they get
wet. However they’re more versatile and easier to put on for actions that require
more dexterity. We’ve used gear and gear from all the prime health manufacturers in our house and business gyms, and we know which companies are respected and which of them you should avoid.
She loves that CrossFit is infinitely scalable for any
athlete. It is so enjoyable seeing a neighborhood full the
identical workout, but in their own means based their capacity and strength.
Megan at present lives in University Place along with
her three cats – Leonardo DiCatpurrrio, Kat Winslet and Loaf Goodson.
For these conversant in CrossFit benchmarks, this exercise looks like Fran meets a high-skill
chipper—fast, intense, and unforgiving if you lose control of your respiratory or grip.
For these not so in tune with CrossFit, prepare to be examined in a challengingly enjoyable means.
Even if you’re not aiming for the CrossFit
Video Games, 25.2 is value making an attempt. The train combos problem even seasoned CrossFitters and dedicated gym-goers seeking to
check their expertise. Mastering 25.2 calls for solid method, strategic pacing, and mental toughness.
Poor transitions add unnecessary fatigue and cost useful seconds, which add
up over a 12-minute workout. Elite athletes purpose for
sub-one-minute rounds early, while intermediate athletes should persist with second intervals to keep away from excessive fatigue.
Maintaining a gradual EMOM-style pace helps ensure a powerful push in later
rounds. A wholesome life-style needs to be manageable and realistic for the lengthy term.
When they developed a passion for CrossFit and determined that
they had been ready for a extra intentional life path,
a CrossFit fitness center was at the heart of their new profession goals.
Ashleigh and her family have lived throughout the country following Jon’s corporate
profession and have now settled again in University Place ready
to serve the group they love. Ashleigh has been teaching CrossFit for 5 years and is a Degree 2 CrossFit Coach and has her CrossFit Youngsters Certificate.
She is worked up about helping individuals achieve their personal fitness goals.
Chris ultimately made his method to University
Place CrossFit and knew that he was on the proper place.
Chris is a Stage 1 CrossFit Trainer and has his CrossFit Masters Coach Certificates.
The finest gymnastics grips for CrossFit aren’t needed for
each exercise or movement. The last workout of the 2025 CrossFit Open has been revealed, and it’s a real test
of practical health.
We offer totally different memberships suitable for different ranges of dedication and finances.
The most popular ones are Bear KompleX, PICSIL, and Victory Grips.
These brands are recognized for producing high-quality, durable grips in a quantity of styles to
go nicely with athletes with totally different hand sizes and who prefer roughly hand
coverage. Additionally, you don’t need the finger holes to be too close to your palms.
They should sit greater up on your fingers, permitting you to create a dowel impact.
The Victory Tactical Freedom grips are the best no-hole pull-up grips for
CrossFit as a outcome of their sturdiness, the quantity of coverage they offer, and their grippiness.
Like the Element 26 grips above, the Victory Tactical Freedom Grips don’t
require any chalk, so that you won’t waste treasured time chalking up your arms
in the center of your workout. For those that choose to maintain their grips on throughout barbell movements,
the JerkFit WODies are a fantastic selection. They characteristic a three-inch wrist strap that gives help for thrusters, jerks, and snatches.
I also like that the finger loops make these grips easier to take on and off.
If you don’t want them on for barbell actions, double unders, or any other motion that requires extra
dexterity, you won’t waste time getting the grips off your fingers.
Too tight grips will pull on your wrists and fingers (if they have finger
holes), digging into your skin and causing irritation. Whereas you could think brief grips appear and feel fantastic
if you first put them on, you’ll notice the poor match
if you leap up to the pull-up bar, and the grips
don’t have a lot flexibility. Grips without finger holes are more handy to use in a WOD.
Your point of view caught my eye and was very interesting. Thanks. I have a question for you.
So whilst you may count on to feel soreness in your glutes and
hamstrings after doing deadlifts, don’t be surprised when you additionally feel your exercise in your again (specifically, your latissimus dorsi muscle tissue, or lats).
The major muscle tissue labored by stiff leg deadlifts are the glutes, hamstrings and decrease back.
The glutes present stability and energy during the exercise whereas the hamstrings
act as a hinge to help management motion. The decrease again is also engaged to hold up an upright posture all through the
lift. Sumo deadlifts target most of the similar muscles as the standard deadlift however
place higher emphasis on the inner thighs and adductors.
This variation can profit individuals with longer torsos or limited ankle mobility.
It Is additionally generally utilized by powerlifters, because the
decreased vary of movement permits them to raise heavier weights.
With variations similar to single-leg stiff leg deadlifts or Romanian Deadlifts,
you’ll have the ability to additional problem yourself with this exercise.
Alternate Options such as good mornings or hip thrusts can be used to focus on related muscular tissues labored by the
stiff leg deadlift if needed. All in all, understanding the way to correctly carry out a stiff leg deadlift and
which muscular tissues it really works will assist you to get probably the
most out of your exercise routine.
For example, the hex bar deadlift elicited a really
excessive stage of activation rates in the gluteus
maximus. When testing a 1RM, or completing low-rep, high weight deadlifts, it’s not hard to get pumped and able to shift the bar.
Decreasing the burden you’re lifting to accommodate a excessive rep range for deadlifts, nevertheless,
can feel a bit mundane. Sustaining determination and preserving motivated for top repetition deadlifts could be powerful as you’re repeating the motion many times.
Attempt focussing on being consistent, no matter motivation and you’ll see gains from week to
week. To assist combat this, focus on maintaining your kind pretty much as
good as potential, and permit the potential outcomes of this kind of coaching to
energy you forward by way of each rep and set.
Just make certain to lift according to your talents and remember, making progress is a marathon, not a sprint.
This can result in numbness in the fingers plus ache within the shoulders and neck.
And unhealthy posture could cause this even without lifting heavy
weight which shows how necessary good lifting posture truly is.
Certain you can construct some muscle doing leg curls, rows, pull-ups, and rear delt work.
It isn’t simply the hamstrings that get worked throughout
deadlifts though. Depending on the type of deadlift, your quads and adductor muscle tissue
also get entangled too. Doing deadlifts is amongst the finest approach to exercise your erector spinae since they stretch
and stabilize you throughout the actions.
The erector spinae are literally a group of muscles that run all
the way along either side of your spine. They generally get known as “core muscles” or “lower back muscles”
however those names are deceptive as a result of they
run all the best way from your head to your tailbone.
You ought to always interact your core and keep your backbone in a neutral
place. Execute a sumo deadlift simply as you’ll a traditional deadlift, solely with your ft unfold out extensive, properly outdoors your hands.
This variation, which you’ll feel in your inside thighs, is a superb different when you have bother getting sufficient ankle flexion to perform a conventional deadlift with correct kind.
Deadlifts are a key train that, when carried out proper, will pay off in all elements
of your fitness journey. Deadlifts are highly efficient for selling muscle hypertrophy,
strength, and useful fitness. By activating large muscle groups, including the glutes, hamstrings, quadriceps,
and erector spinae, deadlifts maximize mechanical rigidity and stimulate hypertrophy.